Locking Collars: A Comprehensive Guide to Safety and Efficiency
Introduction
Locking collars are essential components in various industrial, automotive, and construction applications. They provide a secure connection between shafts, providing stability, alignment, and the ability to transmit torque efficiently. Understanding the different types, materials, and uses of locking collars is crucial for safe and optimal performance. This article serves as a comprehensive guide, exploring everything you need to know about locking collars, including their benefits, applications, and best practices.
Types of Locking Collars
There are numerous types of locking collars available, designed for specific applications and shaft sizes. Some common types include:
-
Set Screw Locking Collars: These collars feature a set screw that tightens against the shaft, creating a secure hold. They are suitable for light to medium-duty applications.
-
Clamp Type Locking Collars: These collars consist of two halves that clamp together around the shaft, typically using a lever or screw mechanism. They offer a higher clamping force than set screw collars.
-
Eccentric Locking Collars: These collars have an offset cam that engages with a groove on the shaft, providing a positive locking action. They are commonly used in applications requiring high torque transmission.
-
Split Locking Collars: These collars split into two halves, allowing for easy installation and removal without disassembling the shaft. They are suitable for applications where frequent adjustment is required.
Materials for Locking Collars
The choice of material for a locking collar depends on the specific application and performance requirements. Common materials include:
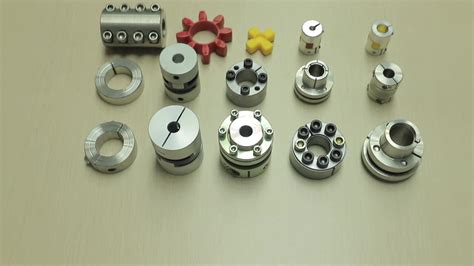
-
Steel: Steel collars offer high strength and durability, making them suitable for heavy-duty applications.
-
Stainless Steel: Stainless steel collars resist corrosion and are ideal for food processing, chemical, and marine environments.
-
Aluminum: Aluminum collars are lightweight and corrosion-resistant, making them suitable for aerospace and automotive applications.
-
Plastic: Plastic collars are low-cost and provide electrical insulation, making them suitable for electrical and electronic applications.
Benefits of Using Locking Collars
Locking collars offer several advantages, including:
-
Secure Connection: Locking collars provide a positive lock between the shaft and the collar, preventing axial or rotational movement.
-
Easy Installation and Removal: Most locking collars can be installed and removed easily using simple tools, minimizing downtime.
-
High Torque Transmission: Proper installation of a locking collar ensures efficient torque transmission, improving equipment performance and reliability.
-
Compact Design: Locking collars have a compact design, allowing for use in tight spaces without compromising performance.
Applications of Locking Collars
Locking collars find applications in a wide range of industries, including:
-
Industrial Machinery: Conveyors, pumps, gearboxes, and other industrial equipment.
-
Automotive: Steering systems, suspension components, and engine accessories.
-
Construction: Scaffolding, formwork, and concrete reinforcement systems.
-
Electrical and Electronic: Wire management, cable supports, and circuit breaker panels.
Best Practices for Using Locking Collars
To ensure optimal performance and safety when using locking collars, follow these best practices:

-
Select the Right Type and Material: Choose a locking collar that is appropriate for the application requirements, shaft size, and environmental conditions.
-
Proper Installation: Follow the manufacturer's instructions for installing the locking collar correctly, ensuring a secure fit without overtightening.
-
Regular Inspection: Regularly inspect locking collars for wear, damage, or proper alignment to ensure continued performance and safety.
-
Tightening Torque: Use a torque wrench to tighten locking collars to the manufacturer's specified torque value, preventing under- or overtightening.
Stories and Lessons Learned
Story 1:
In a manufacturing plant, a conveyor system experienced frequent breakdowns due to loose shaft connections. The use of improper locking collars led to the shafts slipping out of alignment, causing downtime and lost production. Implementing high-quality locking collars with proper installation and tightening torque resolved the issue, significantly reducing breakdowns and improving productivity.

Lesson: Choosing the right locking collar and installing it correctly is crucial for optimal performance and equipment reliability.
Story 2:
In an automotive assembly line, faulty locking collars on suspension components resulted in a recall of thousands of vehicles. The recall was due to inadequate clamping force caused by incorrect torque application. Re-tightening the locking collars to the specified torque value corrected the issue, ensuring the safety and reliability of the vehicles.
Lesson: Proper tightening torque is essential for locking collars to perform as intended, preventing accidents and costly repairs.
Story 3:
In a construction project, scaffolding collapsed due to improper installation of locking collars. Mishandling during assembly caused the collars to loosen, leading to the failure of the scaffolding structure. Regular inspection and training on proper locking collar installation prevented similar incidents in the future.

Lesson: Training and supervision are vital to ensure that locking collars are installed and maintained correctly, minimizing the risk of accidents and costly damage.
Effective Strategies for Using Locking Collars
-
Choose Quality Collars: Invest in high-quality locking collars from reputable manufacturers, ensuring durability and reliability.
-
Use the Right Tools: Use a torque wrench for proper tightening, preventing overtightening or undertightening.
-
Inspect Regularly: Conduct regular inspections of locking collars, identifying any signs of wear or damage for timely repair or replacement.
-
Train Employees: Train personnel on the proper selection, installation, and maintenance of locking collars, promoting safety and efficiency.
-
Follow Manufacturer's Instructions: Adhere to the manufacturer's guidelines for installing and tightening locking collars, guaranteeing optimal performance.
Pros and Cons of Using Locking Collars
Pros:
-
Secure Connection: Locking collars provide a positive lock between shafts, ensuring stability and preventing unwanted movement.
-
Easy Installation and Removal: Most locking collars can be installed and removed quickly and easily, minimizing downtime during maintenance.
-
High Torque Transmission: Properly installed locking collars enable efficient torque transmission, reducing wear and tear on equipment components.
-
Compact Design: Locking collars have a compact design, allowing for use in tight spaces without obstructing other components.
Cons:
-
Potential for Damage: Improper installation or overtightening can damage the shaft or locking collar, leading to costly repairs or replacements.
-
Cost: Locking collars can be more expensive than simple shaft collars, especially for high-performance applications.
-
Maintenance: Regular inspection and tightening of locking collars are essential to maintain optimal performance and prevent accidents.
-
Application Limitations: Some applications may require more specialized shaft locking solutions, such as shrink discs or keyways.
Call to Action
Locking collars are essential components in a wide range of applications, providing secure shaft connections, high torque transmission, and ease of use. By understanding the different types, materials, and best practices for using locking collars, you can maximize their benefits and minimize potential risks. Select quality locking collars, follow manufacturer's instructions, and implement effective maintenance strategies to ensure optimal performance, safety, and cost-effectiveness in your applications.