Thrust Washers: A Comprehensive Guide
What is a Thrust Washer?
A thrust washer is a thin, ring-shaped component used to mitigate axial loads and reduce friction between moving parts in machinery. It is typically made of materials with low coefficients of friction, such as PTFE, nylon, or bronze. Thrust washers find applications in various industries, including automotive, aerospace, and manufacturing.
Functions of a Thrust Washer
-
Load Distribution: Thrust washers distribute axial loads over a larger surface area, reducing the stress concentration and preventing premature bearing failure.
-
Friction Reduction: The low-friction materials used in thrust washers minimize friction between surfaces in contact, enhancing efficiency and reducing energy losses.
-
Stabilization: Thrust washers provide stability to rotating and sliding components, preventing axial displacement and ensuring proper alignment.
-
Noise Reduction: By reducing friction and vibration, thrust washers contribute to noise reduction in machinery.
Types of Thrust Washers
Thrust washers come in various types, each designed for specific applications:
-
Plain Thrust Washers: Flat, cylindrical washers with no special features. They are commonly used in low-load applications and are relatively inexpensive.
-
Tapered Thrust Washers: Washers with a tapered surface on one or both sides. They are suitable for higher loads and can accommodate misalignment.
-
Spherical Thrust Washers: Washers with a spherical surface on one side. They compensate for angular misalignment and are used in high-precision applications.
-
Thrust Ball Bearings: Assemblies of small balls held in a cage between two bearing rings. They offer high load capacity and low friction in demanding applications.
Materials for Thrust Washers
The material of a thrust washer is critical to its performance. Common materials include:
-
PTFE: High temperature resistance, low coefficient of friction, and excellent wear resistance.
-
Nylon: Good surface hardness, toughness, and corrosion resistance.
-
Bronze: High load capacity, anti-friction properties, and good thermal conductivity.
-
Stainless Steel: Strong, corrosion-resistant, and can handle higher loads.
-
Carbon Steel: Versatile and economical, but may require additional lubrication.
Applications of Thrust Washers
Thrust washers are used in a wide range of applications, including:
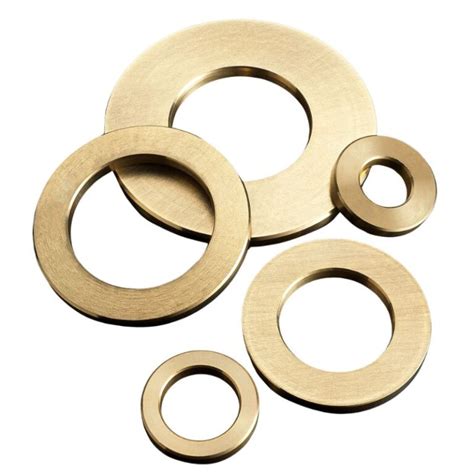

- Automotive: Transmissions, differentials, and engine bearings.
- Aerospace: Jet engines, helicopter gearboxes, and control components.
- Manufacturing: Pumps, compressors, machine tools, and conveyor systems.
- Construction: Excavators, cranes, and other heavy machinery.
Effective Strategies for Using Thrust Washers
-
Choose the Right Material: Consider the operating conditions, load requirements, and desired friction level.
-
Proper Lubrication: Ensure proper lubrication to minimize friction and extend the lifespan of the washer.
-
Precise Installation: Follow specified tolerances and assembly instructions for optimal performance.
-
Regular Maintenance: Monitor thrust washers for wear and damage, and replace them as needed to maintain reliability.
Common Mistakes to Avoid
-
Using the Wrong Material: Selecting a material that is not suitable for the application can lead to premature failure.
-
Improper Lubrication: Insufficient or excessive lubrication can compromise the performance and durability of the washer.
-
Incorrect Installation: Improper installation, such as using the wrong orientation or insufficient torque, can damage the washer or lead to bearing failure.
-
Overloading: Applying excessive loads beyond the washer's capacity can cause deformation or premature failure.
Step-by-Step Approach to Using Thrust Washers
-
Determine the Load and Operating Conditions: Establish the axial load and environmental factors that the washer will encounter.
-
Select the Material and Type: Based on the load and conditions, choose the appropriate material and type of thrust washer.
-
Design the Mounting Surfaces: Ensure the mounting surfaces are flat, parallel, and within specified tolerances.
-
Lubricate the Surfaces: Apply a suitable lubricant to the mounting surfaces and the thrust washer.
-
Install the Washer: Carefully align and install the washer to the specified torque.
-
Verify Alignment and Proper Operation: Check the alignment and performance of the assembly to ensure optimal operation.
Comparing Pros and Cons of Different Materials
Material |
Pros |
Cons |
PTFE |
Low friction, wear resistance, high temperature tolerance |
Low load capacity |
Nylon |
High hardness, toughness, corrosion resistance |
Can deform under high loads |
Bronze |
High load capacity, anti-friction properties, good thermal conductivity |
Higher cost |
Stainless Steel |
Strong, corrosion-resistant, high load capacity |
High friction |
Carbon Steel |
Versatile, economical |
May require additional lubrication |
Benefits of Using Thrust Washers
- Reduced Friction and Energy Losses
- Increased Load Capacity and Bearing Life
- Enhanced Stability and Alignment
- Reduced Noise and Vibration
- Improved Overall Efficiency and Reliability
Statistics on the Use of Thrust Washers
According to a study by the American Bearing Manufacturers Association (ABMA), the global thrust washer market is projected to reach $1.2 billion by 2025. The growing demand for thrust washers is driven by the increasing use of high-speed machinery, demanding aerospace applications, and the need for energy-efficient solutions.
Table 1: Thrust Washer Market Share by Application

Application |
Market Share |
Automotive |
45% |
Aerospace |
25% |
Manufacturing |
20% |
Construction |
10% |
Table 2: Top Thrust Washer Manufacturers by Revenue
Manufacturer |
Revenue (USD million) |
SKF |
350 |
NSK |
275 |
Timken |
220 |
NTN |
175 |
FAG |
150 |
Table 3: Recent Trends in Thrust Washer Technology
Trend |
Description |
Advanced Materials |
Development of new materials with improved friction, wear resistance, and load capacity. |
Coatings and Surface Treatments |
Application of coatings and surface treatments to enhance performance and extend lifespan. |
Self-Lubricating Washers |
Thrust washers with built-in lubrication systems for maintenance-free operation. |
Condition Monitoring |
Integration of sensors and monitoring systems to track the health of thrust washers. |
Conclusion
Thrust washers play a vital role in machinery by mitigating axial loads, reducing friction, and enhancing performance. Choosing the right material, type, and using proper installation techniques are crucial for maximizing their effectiveness. By following the strategies and avoiding common mistakes, engineers can harness the benefits of thrust washers to improve the reliability, efficiency, and longevity of their machinery.
