The Ultimate Guide to Cotters and Cotter Pins: A Comprehensive Encyclopedia
Introduction
Cotters and cotter pins are essential mechanical components used in a wide range of industries for securing and aligning various components. Understanding their properties, applications, and best practices is crucial for engineers, technicians, and DIY enthusiasts alike. This comprehensive encyclopedia will provide an in-depth exploration of cotters and cotter pins, empowering you with the knowledge to make informed decisions in your projects.
Types of Cotters
There are several types of cotters, each designed for specific applications:
-
Taper Pins: Cylindrical pins with a tapered end, used to lock components together.
-
Split Pins: Also known as cotter pins, these consist of a split cylindrical body and two arms.
-
Gib Head Cotters: Have a wedge-shaped head on one end and a tapered shaft on the other, used to adjust the position of components.
-
Plunger Cotters: Used as spring plungers to hold components in place.
Materials
Cotters and cotter pins are typically made of:
-
Steel: Strong and durable, suitable for most applications.
-
Stainless Steel: Resistant to corrosion, making them ideal for harsh environments.
-
Brass: Provides good electrical conductivity and is non-magnetic.
Applications
Cotters and cotter pins find applications across various industries, including:


-
Automotive: Securing piston pins, connecting rods, and other components.
-
Aerospace: Fastening aircraft assemblies and control surfaces.
-
Construction: Connecting structural elements and securing scaffolding.
-
Manufacturing: Align and hold components during machining and fabrication.
-
HVAC: Securing pipes, ducts, and equipment.
Selection Criteria
Choosing the right cotter or cotter pin requires consideration of factors such as:
-
Material: Select the material based on the application environment and durability requirements.
-
Size: Ensure the cotter fits snugly into the hole or groove.
-
Type: Choose the appropriate type based on the application requirements.
-
Load Capacity: Consider the forces the cotter will experience.
-
Temperature Resistance: Ensure the cotter can withstand the operating temperatures.
Installation and Removal
Installation:
- Clean the hole or groove and the cotter.
- Insert the cotter into the hole by tapping it gently with a hammer.
- Check if the cotter is seated securely.
Removal:

- Use a cotter pin remover or a screwdriver to pry the split ends of the cotter pin open.
- Push the cotter pin out of the hole using a punch.
Best Practices
For optimal performance and safety, follow these best practices:
- Use the appropriate type and size of cotter for the application.
- Ensure the hole or groove is clean and free of burrs.
- Lubricate the cotter to reduce friction and prevent seizure.
- Regularly inspect cotters and cotter pins for wear or damage.
- Replace cotters or cotter pins immediately if damaged or worn.
Troubleshooting Common Problems
Cotter or Cotter Pin Not Fitting:
- Check the size and type of cotter.
- Clean the hole or groove thoroughly.
Cotter or Cotter Pin Falling Out:
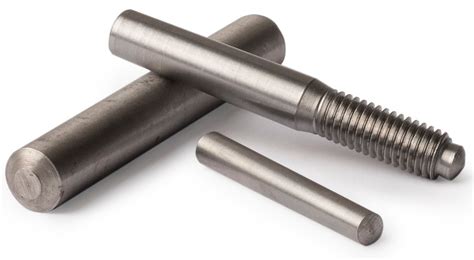
- Ensure the cotter is seated securely.
- Consider using a locking cotter pin or a retaining compound.
Cotter or Cotter Pin Breaking:
- Check if the cotter is overloaded or incorrectly installed.
- Select a cotter with a higher load capacity or a different material.
Effective Strategies
To maximize the effectiveness of cotters and cotter pins:
- Choose the correct material and type based on the application requirements.
- Install and remove cotters and cotter pins properly to ensure optimal performance.
- Regularly inspect and maintain cotters and cotter pins to prevent failures.
Tips and Tricks
- Use a cotter pin spreader to easily open split ends.
- Apply a drop of threadlocker to the cotter to prevent loosening.
- Keep a variety of cotters and cotter pins in your toolbox for different applications.
Comparison of Pros and Cons
Type |
Pros |
Cons |
Taper Pins |
Strong and secure |
Difficult to remove |
Split Pins |
Easy to install and remove |
Can loosen over time |
Gib Head Cotters |
Adjustable |
Require a groove for installation |
Plunger Cotters |
Act as spring plungers |
Not suitable for high loads |
Call to Action
Whether you're an experienced engineer or a DIY enthusiast, understanding cotters and cotter pins is essential for successful project outcomes. This encyclopedia provides comprehensive information to guide you in your selection, installation, and maintenance practices. Utilize the knowledge gained here to ensure the reliability and safety of your mechanical systems.