The Ultimate Guide to Locking Collars: Ensuring Precision, Safety, and Control in Industrial Applications
Introduction
Locking collars, also known as shaft collars or split collars, are essential components in a wide range of industrial applications. They provide a secure and reliable means of securing components onto shafts, preventing axial movement and maintaining precise alignment. This comprehensive guide will delve into the intricacies of locking collars, providing an in-depth exploration of their types, applications, benefits, and considerations for optimal performance.
Types of Locking Collars
Locking collars come in various types, each designed to meet specific application requirements. Here's a detailed overview of the most common types:
-
Single-Screw Locking Collar: Features a single screw that tightens against the shaft, providing secure clamping.
-
Double-Screw Locking Collar: Utilizes two screws to evenly distribute clamping force, offering increased holding capacity and stability.
-
Quick-Release Locking Collar: Allows for rapid installation and removal with a simple push-pull mechanism.
-
Split Locking Collar: Consists of two halves that clamp together around the shaft, providing a versatile and easy-to-use solution.
-
Heavy-Duty Locking Collar: Designed to withstand high torque and axial loads, ideal for demanding industrial applications.
Applications of Locking Collars
The versatility of locking collars extends across numerous industries and applications, including:
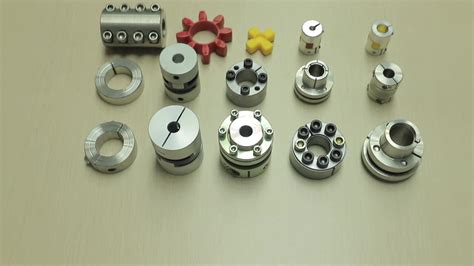
-
Machine Tooling: Securing gears, pulleys, and other components on machine shafts.
-
Linear Motion Systems: Maintaining axial positioning of bearings, slides, and other linear motion components.
-
Conveyor Systems: Preventing belt slippage and ensuring accurate alignment of rollers and sprockets.
-
Hydraulic and Pneumatic Systems: Securing pipes, fittings, and hoses to prevent axial movement and maintain pressure integrity.
-
Automation Equipment: Positioning sensors, actuators, and other devices on robot arms and other automated systems.
Benefits of Locking Collars
Incorporating locking collars into industrial applications offers several advantages:
-
Enhanced Precision: Precisely control axial positioning of components, ensuring proper alignment and minimizing vibration.
-
Increased Safety: Securely lock components in place, preventing accidental movement and reducing the risk of accidents.
-
Improved Efficiency: Minimize downtime by ensuring components remain securely positioned, reducing the need for frequent adjustments or repairs.
-
Cost Savings: Reduce maintenance costs by eliminating premature component wear and failure due to improper alignment or movement.
-
Simplified Maintenance: Easy to install and remove, allowing for quick component changes and maintenance tasks.
Considerations for Choosing Locking Collars
When selecting locking collars, consider the following factors:
-
Shaft Diameter: Choose collars that match the diameter of the shaft to ensure a snug fit.
-
Clamping Force: Determine the required clamping force based on the application's load requirements.
-
Material: Consider the material of the collar to withstand the operating environment, such as temperature, corrosion, and chemical resistance.
-
Mounting Style: Choose collars with the appropriate mounting style (set screw, quick-release, etc.) to suit the application.
-
Industry Standards: Adhere to industry standards, such as ISO or DIN, to ensure compatibility with other components and facilitate maintenance.
Stories and Lessons Learned
Stories of successful locking collar applications can provide valuable insights:
-
Case Study 1: A manufacturing facility reduced downtime by 30% by implementing locking collars to secure gears on conveyor belts, preventing alignment issues that caused frequent belt slippage.
-
Case Study 2: A robotics company enhanced the precision of its automated assembly line by utilizing locking collars to precisely position sensors and actuators, resulting in a 20% increase in production efficiency.
-
Lesson Learned: Proper selection and application of locking collars can significantly improve operational efficiency and reduce maintenance costs in industrial settings.
Pros and Cons of Using Locking Collars
Pros:
- Enhanced precision and reliability
- Increased safety and stability
- Improved efficiency and cost savings
- Versatility and ease of use
Cons:
- May increase overall component cost
- Requires periodic inspection and maintenance
- Not suitable for applications with frequent axial adjustment
Call to Action
Unlock the full potential of your industrial applications with the precision and reliability of locking collars. Explore our comprehensive inventory today and consult with our experts to determine the ideal locking collars for your specific needs. Elevate your operations to new heights of efficiency, safety, and control!

Appendix: Tables
Table 1: Common Locking Collar Types and Applications
Locking Collar Type |
Applications |
Single-Screw |
Machine tooling, linear motion |
Double-Screw |
High-torque applications, heavy machinery |
Quick-Release |
Rapid assembly and disassembly, automation equipment |
Split |
Versatile, easy to install and remove |
Heavy-Duty |
High-load industrial applications, conveyors |
Table 2: Locking Collar Clamping Force and Material Options
Clamping Force (lbs) |
Material Options |
50 - 500 |
Steel, Stainless Steel |
500 - 1000 |
Alloy Steel, Aluminum |
1000+ |
Hardened Steel, Bronze |
Table 3: Comparison of Locking Collar Mounting Styles
Mounting Style |
Advantages |
Disadvantages |
Set Screw |
Secure clamping, high holding capacity |
Requires tools to install |
Quick-Release |
Rapid installation and removal |
May not provide as secure clamping |
Push-On |
Easy to install and remove |
May not be suitable for high-load applications |