Locking Collars: An Essential Guide for Precision Shaft Positioning
Introduction
Locking collars play a crucial role in various industrial and scientific applications, providing secure and accurate shaft positioning. This comprehensive guide delves into the significance of locking collars, their types, selection criteria, effective strategies, common mistakes to avoid, and a step-by-step approach to their installation and use.
Importance and Benefits of Locking Collars
Locking collars offer several advantages in shaft positioning, including:
-
Enhanced Stability: They firmly secure shafts in place, preventing axial and rotational movement.
-
Precision Positioning: The collars enable precise alignment and adjustment of shafts, ensuring optimal performance and accuracy.
-
Reduced Vibration and Noise: By eliminating unwanted movement, locking collars minimize vibration and noise, improving overall system efficiency.
-
Increased Safety: They provide a safe and controlled environment by preventing unintended shaft movement, which could pose safety hazards.
-
Simplified Maintenance: Locking collars simplify maintenance tasks by allowing for quick and easy shaft adjustments or replacements.
Types of Locking Collars
1. Set Screw Collars
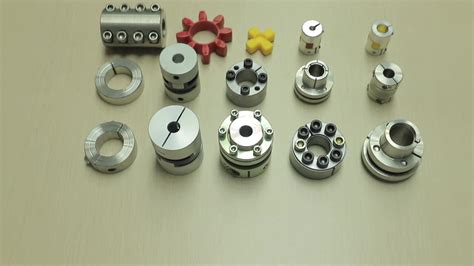
-
Mechanism: Clamped onto the shaft using set screws that tighten against the shaft surface.
-
Advantages: Easy to install and remove, low cost.
-
Disadvantages: May damage the shaft surface, not suitable for high-torque applications.
2. Clamping Collars
-
Mechanism: Tightened around the shaft using a central screw or lever, creating radial compression.
-
Advantages: High holding power, minimizes shaft damage, suitable for heavy-duty applications.
-
Disadvantages: Requires more space than set screw collars, may require additional components for alignment.
3. Expansion Collars
-
Mechanism: Expands to grip the shaft when tightened, typically using a tapered split design.
-
Advantages: High holding power, easy to install and remove without tools, suitable for precise alignment.
-
Disadvantages: May require frequent retightening, not suitable for high-impact applications.
Selecting the Right Locking Collar
Choosing the appropriate locking collar depends on several factors:
-
Shaft Diameter: The collar must match the diameter of the shaft it will be securing.
-
Material: Consider the operating environment and the type of shaft being used.
-
Application: Determine the level of holding power, precision, and alignment required.
-
Space Constraints: Select a collar that fits the available space and allows for necessary adjustments.
-
Cost: Evaluate the cost of the collar in relation to the overall project budget.
Effective Strategies for Using Locking Collars
- Use the correct locking collar for the specific application.
- Ensure that the shaft is clean and free of burrs or debris.
- Tighten the collar securely, but do not overtighten.
- Use a torque wrench for precise tightening, following the manufacturer's recommendations.
- Retighten the collar periodically, especially after initial installation or during heavy-duty use.
Common Mistakes to Avoid
-
Overtightening: Excessive tightening can damage the shaft or the collar, reducing holding power.
-
Undertightening: Insufficient tightening may result in the collar becoming loose, leading to shaft movement.
-
Using Incorrect Size: Selecting a collar with an inappropriate diameter will not provide proper holding or alignment.
-
Ignoring Alignment: Ensure that the collar is correctly aligned with the shaft to avoid excessive stress or binding.
-
Neglecting Maintenance: Periodic inspection and retightening are essential to maintain optimal holding power and prevent accidents.
Step-by-Step Approach to Using Locking Collars
Materials:

- Locking collar
- Torque wrench
- Thread locker (optional)
Steps:
-
Clean the Shaft: Remove any dirt, oil, or debris from the shaft.
-
Slide on the Collar: Align the collar with the desired position on the shaft.
-
Tighten the Collar: Using the torque wrench, tighten the collar to the specified torque value.
-
Apply Thread Locker (Optional): If desired, apply thread locker to the tightening screws to prevent loosening.
-
Retighten Periodically: Check the collar's tightness regularly and retighten as needed.
Why Locking Collars Matter
Locking collars are essential for a wide range of applications, including:
-
Machine Tooling: Precise positioning of cutting tools and spindles.
-
Motion Control Systems: Secure mounting of shafts in robotic arms or automated machinery.
-
Precision Measurement Equipment: Accurate alignment of optical components or calibration devices.
-
Medical Imaging: Precise positioning of patient positioning systems or imaging equipment.
-
Aerospace and Defense: Secure mounting of components in aircraft or weapons systems.
Table 1: Applications and Benefits of Locking Collars
Application |
Benefits |
Machine Tooling |
Enhanced precision and reduced vibration |
Motion Control Systems |
Improved stability and safety |
Precision Measurement Equipment |
Highly accurate shaft positioning |
Medical Imaging |
Patient safety and accurate imaging |
Aerospace and Defense |
Increased reliability and reduced maintenance |
Table 2: Comparison of Locking Collar Types
Type |
Mechanism |
Holding Power |
Ease of Installation |
Cost |
Set Screw Collar |
Tightened with set screws |
Moderate |
Easy |
Low |
Clamping Collar |
Central screw or lever |
High |
Requires alignment components |
Medium |
Expansion Collar |
Expands to grip shaft |
High |
Easy, tool-free |
High |
Table 3: Tips for Choosing the Right Locking Collar
Factor |
Considerations |
Shaft Diameter |
Match the collar diameter to the shaft |
Material |
Select a material compatible with the shaft and environment |
Application |
Determine the level of holding power, precision, and alignment required |
Space Constraints |
Choose a collar that fits the available space |
Cost |
Consider the cost of the collar and installation |
Conclusion
Locking collars are versatile and essential components that play a crucial role in ensuring secure and precise shaft positioning. By understanding their types, selecting the appropriate collar, and following effective strategies, engineers and technicians can optimize the performance and reliability of various industrial and scientific applications. Neglecting or misusing locking collars can compromise safety and equipment functionality, emphasizing the importance of their proper use and maintenance.