Locking Collars: An In-Depth Guide for Secure and Precise Positioning
Introduction
Locking collars, also known as shaft collars, are essential components in various mechanical applications, providing a secure and precise method for positioning and retaining components on shafts. They offer a wide range of benefits, including:
-
Accurate positioning: Locking collars allow for precise adjustment and positioning of components along a shaft, ensuring optimal performance and alignment.
-
Secure locking: The locking mechanism ensures a firm grip on the shaft, preventing components from slipping or rotating unintentionally.
-
Versatile applications: Locking collars are suitable for a wide range of shaft sizes and materials, making them adaptable to various industrial and manufacturing settings.
Types of Locking Collars
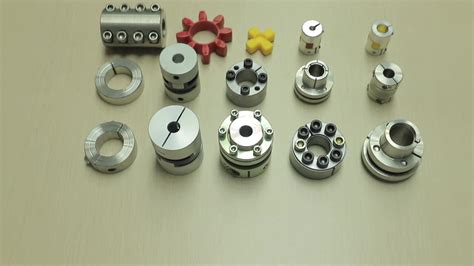
Locking collars come in various types, each designed to meet specific application needs:
-
Set screw locking collars: These collars use one or more set screws to secure them onto the shaft. They are simple to install and adjust, but may require periodic retightening.
-
Clamp locking collars: These collars feature a hinged clamp that tightens around the shaft. They offer a quick and easy installation process and are suitable for applications requiring frequent adjustments.
-
Eccentric locking collars: These collars have an offset cam that locks onto the shaft. They provide a high degree of locking force and are ideal for applications involving high loads or vibrations.
-
Split locking collars: These collars are split into two halves, allowing for easy installation and removal. They are suitable for applications where space is limited or when components need to be positioned very close to each other.
Factors to Consider When Selecting a Locking Collar

When selecting a locking collar, several factors should be considered:
-
Shaft size: The locking collar should be compatible with the diameter of the shaft it will be used on.
-
Material: Locking collars are available in various materials, including steel, stainless steel, and aluminum. The choice of material depends on the specific application requirements, such as corrosion resistance or strength.
-
Clamping force: The clamping force of the locking collar should be sufficient to securely hold the component in place, considering the load and vibration levels it will be subjected to.
-
Adjustability: Some applications may require frequent adjustments, while others may not. The adjustability of the locking collar should be considered based on the application's specific needs.
-
Ease of installation: The ease of installation is important, especially in situations where frequent adjustments or component changes are required.
Table 1: Comparison of Locking Collar Types
Type of Locking Collar |
Advantages |
Disadvantages |
Set screw locking collar |
Simple design, easy to adjust |
May require periodic retightening |
Clamp locking collar |
Quick installation, suitable for frequent adjustments |
May not provide as secure a lock as other types |
Eccentric locking collar |
High clamping force, ideal for high loads |
Can be more difficult to install |
Split locking collar |
Easy installation and removal, suitable for limited space |
May have a lower clamping force than other types |
Applications of Locking Collars
Locking collars are used in a wide range of applications across various industries, including:
-
Machinery: Positioning gears, pulleys, couplings, and other components on shafts in machinery.
-
Robotics: Securing actuators, motors, and other components in robotic systems.
-
Agricultural equipment: Locking components in place on shafts in tractors, harvesters, and other agricultural machinery.
-
Automotive industry: Positioning and securing components in engines, transmissions, and other automotive systems.
-
Medical equipment: Ensuring precise positioning of components in medical devices and instruments.
Stories and Lessons Learned
Story 1:
In a manufacturing plant, a locking collar was improperly tightened on a shaft, resulting in a component slipping and causing a machine malfunction. The lesson learned is to always ensure proper installation and tightening of locking collars to prevent accidents and equipment damage.
Story 2:

An engineer designing a robotic system used an incorrect type of locking collar, which led to the robot arm failing to perform as expected during operation. This highlights the importance of selecting the appropriate locking collar type based on the application requirements.
Story 3:
A maintenance technician in a chemical plant had to replace locking collars on a pump shaft that was subject to high vibrations. By choosing locking collars with a high clamping force and eccentric cam, the technician ensured secure positioning of the components, preventing any vibration-related failures.
Effective Strategies for Using Locking Collars
-
Proper installation: Follow the manufacturer's instructions for installing the locking collar on the shaft. Use the appropriate tightening torque to ensure a secure hold.
-
Regular maintenance: Periodically inspect locking collars for any signs of wear or damage. Retighten or replace them as necessary to maintain proper operation.
-
Use the correct locking collar type: Select the locking collar type that best suits the application requirements, considering factors such as load, vibration, and adjustability.
-
Lubricate locking collars: Lubricating locking collars can reduce friction and wear, ensuring smooth operation and extending their lifespan.
Step-by-Step Approach to Selecting a Locking Collar
-
Determine the shaft size: Measure or obtain the diameter of the shaft where the locking collar will be used.
-
Consider the application requirements: Identify the specific needs of the application, including the load, vibration levels, and adjustability required.
-
Research and compare types of locking collars: Explore the various types of locking collars available and their advantages and disadvantages to determine which type is best suited for the application.
-
Select the appropriate material: Choose a material that meets the application requirements for strength, corrosion resistance, and other relevant factors.
-
Calculate the required clamping force: Determine the necessary clamping force based on the load and vibration levels the locking collar will be subjected to.
-
Choose the correct size and style: Select a locking collar that fits the shaft size and meets the required style, such as set screw or clamp locking collar.
Table 2: Advantages and Disadvantages of Locking Collar Materials
Material |
Advantages |
Disadvantages |
Steel |
High strength, durable |
Susceptible to corrosion |
Stainless Steel |
Excellent corrosion resistance, durable |
Higher cost |
Aluminum |
Lightweight, corrosion-resistant |
Lower strength |
Brass |
Corrosion-resistant, low friction |
Lower strength, more expensive |
Conclusion
Locking collars are essential components in various mechanical applications, providing secure and precise positioning of components on shafts. By understanding the different types, factors to consider, and effective strategies for using locking collars, you can ensure optimal performance, reliability, and safety in your applications.