Unlocking the Secrets of Locking Collars: A Comprehensive Guide
In the realm of mechanical engineering, precision and reliability are paramount. Locking collars play a crucial role in ensuring these attributes, providing secure and adjustable connections for shafts, linear bearings, and other rotating components. This comprehensive guide delves into the intricacies of locking collars, empowering you with the knowledge to select and apply them effectively.
Defining a Locking Collar
A locking collar, also known as a shaft collar or locking ring, is a mechanical device used to secure and locate components on a shaft. It consists of a split collar or ring that can be tightened around the shaft, preventing axial movement of the associated component. Locking collars are available in various designs, materials, and sizes to accommodate different applications.
Types of Locking Collars
The diverse range of locking collars available can be categorized into several types:
-
Set Screw Collars: These collars feature one or more set screws that are tightened against the shaft to secure the collar.
-
Eccentric Collars: These collars have an eccentrically mounted shaft that can be rotated to lock or release the collar.
-
Clamping Collars: These collars utilize a clamping mechanism, such as a lever or screw, to apply pressure on the shaft and secure the collar.
-
Adapter Collars: These collars are designed to connect shafts of different diameters or materials.
-
Split Collars: These collars are made of two or more segments that are bolted together around the shaft.
Materials Used in Locking Collars
The materials used in locking collars vary depending on the application and performance requirements. Some common materials include:
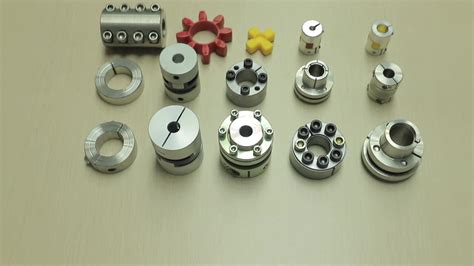
-
Steel: Steel collars provide strength and durability, making them suitable for heavy-duty applications.
-
Stainless Steel: Stainless steel collars offer corrosion resistance, making them ideal for harsh environments.
-
Aluminum: Aluminum collars are lightweight and resistant to corrosion, making them suitable for food processing and other applications where weight is a concern.
-
Plastic: Plastic collars are economical and non-conductive, making them suitable for applications where electrical isolation is required.
Applications of Locking Collars
Locking collars find application in a wide range of industries, including:
-
Machinery and Equipment: Securing gears, bearings, and other components on shafts.
-
Automotive: Locating and securing components in drivetrains and suspensions.
-
Aerospace: Ensuring the secure and precise positioning of components in aircraft and spacecraft.
-
Medical Devices: Providing accurate and reliable connections in medical equipment.
-
Food Processing: Facilitating easy cleaning and maintenance by allowing for the quick removal of components.
Selecting the Right Locking Collar
Choosing the right locking collar for a specific application requires careful consideration of several factors:

-
Shaft Diameter: The collar must be the correct size to fit the diameter of the shaft.
-
Material: The collar material should be compatible with the application environment and performance requirements.
-
Locking Mechanism: The type of locking mechanism (set screw, eccentric, clamping, etc.) should be selected based on the desired level of security and ease of adjustment.
-
Operating Conditions: The collar should be able to withstand the operating conditions, such as temperature, vibration, and chemical exposure.
Effective Strategies for Using Locking Collars
To ensure optimal performance and longevity of locking collars, consider the following strategies:
-
Use the Proper Torque: Tighten the collar to the recommended torque specification to prevent overtightening and damage.
-
Inspect Regularly: Periodically inspect the collar for signs of wear or damage, especially after prolonged use.
-
Lubricate as Needed: Lubricate the shaft and collar interface to reduce friction and prevent seizure.
-
Avoid Using Damaged Collars: A damaged collar can compromise the security and performance of the connection.
-
Store Properly: Store collars in a dry, well-ventilated area to prevent corrosion and damage.
Tips and Tricks for Locking Collars
Enhance your locking collar knowledge with these helpful tips and tricks:

-
Use a Lock Nut: Combine a locking collar with a lock nut to prevent it from loosening due to vibration or shock.
-
Check for Axial Movement: Ensure there is no axial movement between the collar and the shaft by applying a small amount of force after tightening the collar.
-
Use Multiple Collars: For critical applications, consider using multiple collars spaced apart to provide additional security.
-
Clean the Shaft Surface: Before installing the collar, clean the shaft surface thoroughly to remove any debris that could compromise the connection.
Step-by-Step Approach to Using Locking Collars
Follow these steps to install and use locking collars effectively:
-
Select the appropriate collar: Determine the correct size, material, and locking mechanism for the application.
-
Clean the shaft surface: Remove any dirt, rust, or oil from the shaft surface where the collar will be installed.
-
Slide the collar onto the shaft: Position the collar on the shaft and slide it into place.
-
Tighten the locking mechanism: Use the appropriate tightening tool (wrench, hex key, etc.) to secure the collar in the desired position.
-
Check for axial movement: Apply a small amount of force to the collar to verify that there is no axial movement between the collar and the shaft.
Stories and Lessons Learned
Story 1: A manufacturing facility experienced excessive downtime due to repeated failures of locking collars on their machinery. Upon investigation, it was discovered that the collars were being overtightened, causing them to seize and break. By implementing proper torque specifications and training maintenance personnel, the facility significantly reduced downtime and improved operational efficiency.
Lesson Learned: Overtightening locking collars can lead to premature failure and operational disruptions.
Story 2: An aerospace company encountered difficulties maintaining precise alignment of components in their spacecraft. By switching to locking collars with eccentric locking mechanisms, they gained the ability to微调 the position of components with greater accuracy. This resulted in improved performance and reliability of the spacecraft.
Lesson Learned: Eccentric locking collars offer precise adjustment capabilities, allowing for optimal alignment and component performance.
Story 3: A food processing plant faced challenges with maintaining hygiene standards due to the accumulation of debris on locking collars. By replacing traditional set screw collars with smooth-surfaced clamping collars, they were able to reduce the number of crevices where bacteria could harbor. This resulted in improved sanitation and compliance with regulatory standards.
Lesson Learned: Smooth-surfaced locking collars promote hygiene by preventing the accumulation of debris and promoting easy cleaning.
Conclusion
Locking collars are indispensable components in a wide range of mechanical applications, providing secure and adjustable connections for shafts and other rotating components. By understanding the different types, materials, and applications of locking collars, engineers can select and use them effectively to enhance the performance, reliability, and safety of their designs.
