Mastering the Essential Tool for Shaft Connections: The Locking Collar
In the realm of precision engineering, securing shafts and components with utmost reliability is paramount. Enter the locking collar, an indispensable device that has revolutionized the way these connections are made. This comprehensive guide will provide you with an in-depth understanding of locking collars, their types, applications, and the essential know-how to ensure flawless operation.
Unlocking the Benefits of Locking Collars
Locking collars have gained widespread acceptance for their exceptional performance in a wide range of applications:
-
High Holding Power: Advanced locking mechanisms provide an unwavering grip, ensuring stability and preventing slippage under demanding conditions.
-
Ease of Installation and Removal: Designed for user convenience, locking collars can be quickly installed and removed, minimizing downtime and enhancing efficiency.
-
Versatility: Available in various materials and configurations, locking collars cater to diverse applications, including shaft positioning, axial load transmission, and vibration dampening.
-
Precision and Accuracy: Manufactured to exacting tolerances, locking collars ensure precision alignment and zero backlash, essential for optimal system performance.
Exploring the Array of Locking Collar Types
The world of locking collars encompasses a myriad of designs, each tailored to specific needs:
-
Eccentric Cam Collars: Employing a cam-shaped mechanism, these collars offer rapid tightening and loosening, making them ideal for frequent adjustments.
-
Set Screw Collars: Featuring multiple set screws, these collars provide a robust locking force and are widely used in high-torque applications.
-
Clamp Collars: Utilizing a clamping mechanism, these collars offer exceptional holding power and are commonly used with large shafts or heavy loads.
-
Taper Lock Collars: Relying on a tapered design, these collars provide superior torque transmission and are commonly found in industrial machinery.
-
Threaded Collars: Featuring a threaded bore, these collars are easily mounted on threaded shafts and offer precise positioning.
Navigating the Applications of Locking Collars
The versatility of locking collars extends to a multitude of industries and applications:
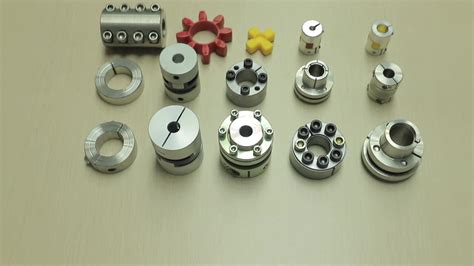
-
Mechanical Engineering: Securing gears, pulleys, and other rotating components on shafts.
-
Automotive Industry: Used in steering systems, powertrains, and suspension components.
-
Aerospace Engineering: Essential for ensuring secure connections in aircraft engines and flight controls.
-
Manufacturing: Utilized in conveyor systems, robotics, and automated equipment.
-
Construction: Employed in concrete formwork, scaffolding, and equipment support structures.
Choosing the Right Locking Collar: A Step-by-Step Approach
Selecting the appropriate locking collar is crucial for optimal performance and longevity:
-
Determine Shaft Size: Measure the diameter of the shaft where the collar will be installed.
-
Identify Application Requirements: Consider the holding power, torque transmission, and environmental conditions required.
-
Choose Locking Collar Type: Select the type of collar that best suits your application (e.g., eccentric cam, set screw, etc.).
-
Check Bore Size: Ensure that the bore diameter of the collar matches the shaft size.
-
Verify Material Compatibility: Choose a collar material that is compatible with the shaft and operating environment.
Pros and Cons of Locking Collars: Weighing the Options
Pros:
-
Exceptional Holding Power: Advanced locking mechanisms ensure a secure connection.
-
Easy Installation and Removal: User-friendly designs minimize downtime and maximize efficiency.
-
Versatility: Wide range of types and sizes available to meet diverse applications.
-
Precision and Accuracy: Manufactured to exacting tolerances, ensuring optimal performance.
Cons:

-
Not Suitable for All Applications: Some applications may require other types of shaft connections.
-
Can Damage Shafts: Overtightening or improper use can lead to damage to the shaft.
-
Maintenance Considerations: Regular inspection and lubrication may be necessary to ensure optimal performance.
Common Mistakes to Avoid When Using Locking Collars
-
Overtightening: Excessive tightening can damage the collar or shaft.
-
Insufficient Tightening: Loose collars can lead to slippage and system failures.
-
Ignoring Maintenance: Regular inspection and lubrication are essential for extending the collar's lifespan.
-
Improper Installation: Follow manufacturer instructions carefully to avoid improper alignment or damage.
-
Using the Wrong Type of Collar: Selecting the incorrect collar type for the application can compromise performance and safety.
FAQs: Addressing Common Locking Collar Concerns
-
Q: Can locking collars be reused? A: Yes, depending on the type of collar and the amount of wear it has experienced.
-
Q: How often should I lubricate a locking collar? A: Refer to the manufacturer's recommendations, which typically range from every few months to annually.
-
Q: What materials are locking collars made of? A: Common materials include steel, aluminum, stainless steel, and nylon.
-
Q: What torque should I use to tighten a locking collar? A: Refer to the manufacturer's specifications, which will vary depending on the collar type and size.
-
Q: How do I remove a stuck locking collar? A: Gently tap the collar with a hammer while applying penetrating oil to loosen it.
-
Q: Can I use locking collars on hollow shafts? A: Yes, but special collars designed for hollow shafts are required.
Conclusion
Locking collars have become an indispensable tool for engineers and technicians across a wide range of industries, providing secure and reliable connections for shafts and components. By understanding the different types, applications, and proper use of locking collars, you can ensure optimal performance and longevity while minimizing costly downtime. Remember to always prioritize safety, follow manufacturer instructions, and seek professional advice when dealing with critical applications.
Tables
Table 1: Common Locking Collar Types and Features
Collar Type |
Mechanism |
Holding Power |
Ease of Installation |
Eccentric Cam |
Cam-shaped |
Moderate |
Excellent |
Set Screw |
Multiple set screws |
High |
Good |
Clamp |
Clamping mechanism |
Exceptionally High |
Moderate |
Taper Lock |
Tapered design |
Superior |
Moderate |
Threaded |
Threaded bore |
Moderate |
Excellent |
Table 2: Locking Collar Applications and Industries
Industry |
Applications |
Mechanical Engineering |
Gears, pulleys, rotating components |
Automotive Industry |
Steering systems, powertrains, suspension |
Aerospace Engineering |
Aircraft engines, flight controls |
Manufacturing |
Conveyors, robots, automated equipment |
Construction |
Concrete formwork, scaffolding, support structures |
Table 3: Comparison of Locking Collar Materials
Material |
Advantages |
Drawbacks |
Steel |
High strength, durability |
Can corrode |
Aluminum |
Lightweight, corrosion-resistant |
Lower strength |
Stainless Steel |
Excellent corrosion resistance, high strength |
More expensive |
Nylon |
Low friction, electrical insulation |
Lower holding power |