Thrust Washers: Your Ultimate Guide to Everything You Need to Know
Introduction
Thrust washers are unsung heroes of the mechanical world, silently preventing wear and friction in countless applications. From heavy machinery to automotive engines, these unassuming components play a crucial role in ensuring smooth operation and extending equipment lifespan.
In this comprehensive guide, we'll delve into the fascinating world of thrust washers, exploring their types, materials, applications, and maintenance tips. Whether you're a seasoned engineer or just curious about these essential mechanical devices, this article is packed with valuable information and insights.
Types of Thrust Washers
The primary function of a thrust washer is to provide a low-friction bearing surface between rotating and axial components. Depending on the specific application, thrust washers come in various types, each with its own unique characteristics:
-
Plain Thrust Washers: These are simple, flat washers that provide a basic sliding surface. They are commonly made of metals like steel or bronze, and can be used in low-load, low-speed applications.
-
Tapered Thrust Washers: These washers have a tapered shape that allows for self-alignment and compensation for misalignment between shafts. They are often used in applications with heavy loads and moderate speeds.
-
Ball Thrust Washers: These washers use balls as rolling elements between the thrust surfaces. They offer lower friction than plain washers and can handle higher speeds and loads.
-
Needle Thrust Washers: These washers use needle rollers as rolling elements. They provide a high load capacity in a compact design, making them suitable for applications with limited space.
Materials for Thrust Washers
The choice of material for a thrust washer is critical, as it determines the washer's durability, load-carrying capacity, and friction properties. Common materials used include:
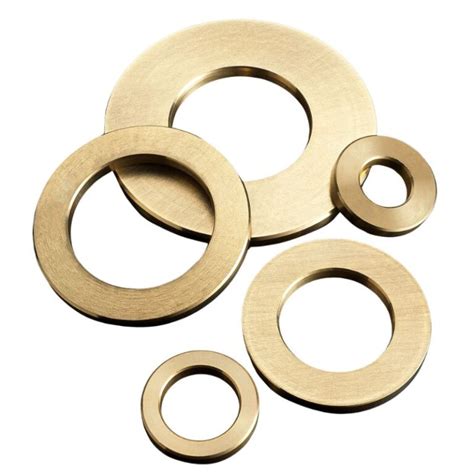
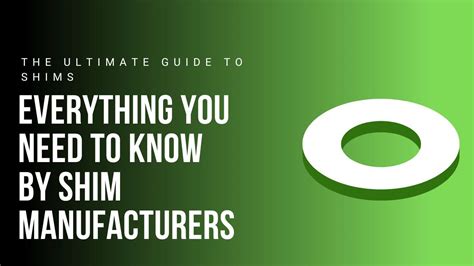
-
Steel: The most common material for thrust washers, offering good strength, wear resistance, and low cost.
-
Bronze: Provides a low-friction surface and resists corrosion, making it suitable for applications where lubrication is limited.
-
Aluminum: Lightweight and resistant to corrosion, but not as strong as steel.
-
Phenolic Resin: A non-metallic material that offers good strength, low friction, and electrical insulation properties.
-
Polymer: A wide range of polymers are used in thrust washers, including PTFE, nylon, and PEEK. They offer low friction, wear resistance, and chemical resistance.
Applications of Thrust Washers
Thrust washers are used in a vast array of applications, including:
-
Automotive Engines: In engines, thrust washers are used to control axial movement of the crankshaft and prevent damage to the cylinder block.
-
Industrial Machinery: Thrust washers are used in gearboxes, pumps, and other industrial machinery to reduce friction and prevent wear between rotating and axial components.
-
Aerospace: Thrust washers are used in aircraft engines and other aerospace applications to handle high loads and extreme temperatures.
-
Power Generation: Thrust washers are used in turbines and generators to support rotating shafts and prevent damage to bearings.
Why Thrust Washers Matter
Thrust washers play a critical role in the performance and lifespan of mechanical equipment. By reducing friction and wear, they:
-
Increase Efficiency: Lower friction means less energy loss, resulting in improved efficiency for machinery.
-
Extend Equipment Life: Reduced wear prolongs the lifespan of components and the equipment itself.
-
Prevent Catastrophic Failure: By preventing excessive wear, thrust washers help prevent sudden and costly failures that can bring operations to a halt.
How to Select the Right Thrust Washer
Choosing the right thrust washer for a specific application requires careful consideration of several factors:

-
Load Capacity: Determine the maximum axial load that the thrust washer will experience.
-
Speed: Consider the operating speed of the equipment to ensure the thrust washer can handle the centrifugal forces.
-
Lubrication: Identify the type and availability of lubrication in the application.
-
Material: Select a material that is compatible with the operating conditions, such as temperature, corrosion, and load.
-
Dimensions: Ensure the thrust washer fits the available space and aligns with the mating components.
Tips and Tricks for Using Thrust Washers
-
Proper Lubrication: Ensure that thrust washers are adequately lubricated to minimize friction and prevent wear.
-
Avoid Overtightening: Do not overtighten bolts or screws when securing thrust washers, as this can cause distortion and reduce their effectiveness.
-
Regular Inspection: Regularly inspect thrust washers for signs of wear, damage, or misalignment.
-
Use High-Quality Materials: Invest in high-quality thrust washers made from durable materials to ensure optimal performance and longevity.
Common Mistakes to Avoid
-
Ignoring Load Capacity: Using a thrust washer with insufficient load capacity can lead to premature failure and damage to other components.
-
Neglecting Lubrication: Inadequate lubrication can cause excessive friction, wear, and overheating.
-
Incorrect Alignment: Misaligned thrust washers can cause uneven wear and reduced effectiveness.
-
Using Incompatible Materials: Choosing a material that is not compatible with the operating conditions can lead to corrosion, wear, or failure.
Conclusion
Thrust washers are humble but essential components that play a vital role in the smooth operation and longevity of mechanical equipment. By understanding the types, materials, applications, and selection criteria for thrust washers, you can ensure that these unassuming heroes are working their magic to prevent friction, extend lifespan, and keep your machinery running smoothly.
Tables
Table 1: Types of Thrust Washers
Type |
Description |
Plain Thrust Washers |
Simple, flat washers with a sliding surface |
Tapered Thrust Washers |
Tapered shape for self-alignment |
Ball Thrust Washers |
Balls as rolling elements for reduced friction |
Needle Thrust Washers |
Needle rollers as rolling elements for high load capacity |
Table 2: Materials for Thrust Washers
Material |
Characteristics |
Steel |
Good strength, wear resistance, low cost |
Bronze |
Low friction, corrosion resistance |
Aluminum |
Lightweight, corrosion resistance |
Phenolic Resin |
Good strength, low friction, electrical insulation |
Polymer |
Low friction, wear resistance, chemical resistance |
Table 3: Applications of Thrust Washers
Industry |
Application |
Automotive |
Engine crankshaft support |
Industrial |
Gearboxes, pumps, machinery |
Aerospace |
Aircraft engines, extreme temperatures |
Power Generation |
Turbines, generators |