The Colossus of Industry: Unveiling the World's Largest Industrial Robots
Industrial robots have revolutionized manufacturing processes worldwide, enabling unparalleled precision, efficiency, and productivity. Among these towering machines, a select few stand out as titans of industry, boasting extraordinary capabilities and sheer size. In this article, we will delve into the realm of these colossal robots, exploring their remarkable features, applications, and the transformative impact they have on modern manufacturing.
Introducing the Largest Industrial Robots
The largest industrial robots in the world are behemoths, towering over their human counterparts and weighing several tons. These machines are often custom-designed to meet the specific demands of heavy-duty industries such as automotive manufacturing, shipbuilding, and aerospace. Here are some of the most notable examples:
#1. Kuka Titan
- Height: 4 meters (13 feet)
- Weight: 2.5 metric tons (5,500 pounds)
- Payload capacity: 1,500 kilograms (3,300 pounds)
#2. Fanuc M-2000iA/400L
- Height: 3.6 meters (12 feet)
- Weight: 2.5 metric tons (5,500 pounds)
- Payload capacity: 1,250 kilograms (2,750 pounds)
#3. ABB IRB 6700
- Height: 3.8 meters (12.5 feet)
- Weight: 2.4 metric tons (5,300 pounds)
- Payload capacity: 1,500 kilograms (3,300 pounds)
#4. Yaskawa Motoman HP20
- Height: 3.2 meters (10.5 feet)
- Weight: 2.1 metric tons (4,600 pounds)
- Payload capacity: 1,200 kilograms (2,600 pounds)
#5. Kawasaki Robotics CP300L
- Height: 2.8 meters (9 feet)
- Weight: 2.0 metric tons (4,400 pounds)
- Payload capacity: 1,000 kilograms (2,200 pounds)
Key Features of the Largest Industrial Robots
These massive machines share several key features that distinguish them from smaller industrial robots:
-
Exceptional Payload Capacity: The largest industrial robots boast impressive payload capacities, allowing them to handle heavy workpieces and components with ease.
-
Extreme Reach: Their extended reach enables them to access hard-to-reach areas in large-scale manufacturing environments.
-
High Precision: Despite their size, these robots maintain remarkable precision, ensuring accurate and repeatable operations.
-
Multi-Axis Articulation: Most large industrial robots feature multi-axis articulation, providing them with flexibility and agility in performing complex tasks.
-
Customizable End Effectors: To accommodate a wide range of applications, these robots can be fitted with various end effectors, such as welding torches, grippers, and spray guns.
Applications of the Largest Industrial Robots
The largest industrial robots are primarily deployed in heavy-duty industries, where their size and capabilities are critical for handling demanding tasks. Some of their common applications include:
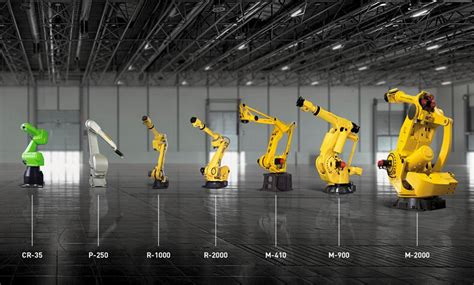

-
Automotive Manufacturing: Assembling vehicles, welding components, and painting bodies.
-
Shipbuilding: Constructing and welding ship hulls, installing engines, and handling heavy parts.
-
Aerospace: Assembling aircraft fuselages, wings, and engines, and performing intricate welding tasks.
-
Metal Fabrication: Cutting, bending, and welding large metal structures.
-
Heavy Construction: Placing concrete beams, assembling bridges, and handling heavy machinery.
Transformative Impact on Manufacturing
The introduction of the largest industrial robots has had a transformative impact on manufacturing processes, bringing about numerous advantages:
-
Increased Productivity: These robots can operate tirelessly for extended periods, significantly increasing production output.
-
Improved Quality: Their precision and accuracy ensure consistent high-quality products.
-
Reduced Costs: By automating labor-intensive tasks, large industrial robots can reduce labor costs and improve overall efficiency.
-
Enhanced Safety: Removing humans from hazardous environments improves workplace safety.
-
New Possibilities: The capabilities of these robots enable the exploration of new and innovative manufacturing techniques.
Potential Drawbacks of the Largest Industrial Robots
Despite their advantages, large industrial robots also have potential drawbacks that should be considered:
-
High Initial Investment: Acquiring and integrating these robots into production lines can be expensive.
-
Complexity and Maintenance: Their size and complexity require specialized maintenance and technical expertise.
-
Limited Flexibility: Large industrial robots may not be suitable for highly flexible manufacturing environments.
-
Space Requirements: Their large size requires ample floor space and proper infrastructure.
-
Retraining Needs: Implementing these robots may necessitate retraining of staff to operate and maintain them.
Effective Strategies for Utilizing Large Industrial Robots
To maximize the benefits of large industrial robots, manufacturers should adopt effective strategies:

-
Careful Assessment: Determine the specific needs and requirements of the manufacturing process before investing in a large industrial robot.
-
Proper Training: Provide comprehensive training to operators and maintenance personnel to ensure efficient and safe operation.
-
Integration Planning: Plan the integration of the robot into the production line carefully, considering space requirements, workflow, and safety measures.
-
Regular Maintenance: Establish a rigorous maintenance schedule to prevent downtime and ensure optimal performance.
-
Continuous Improvement: Regularly monitor the performance of the robot and identify opportunities for process optimization and improvement.
Common Mistakes to Avoid with Large Industrial Robots
To avoid common pitfalls, manufacturers should be aware of the following mistakes:
-
Overestimating Capabilities: Avoid assuming that large industrial robots can perform all tasks. Assess their limitations and select the appropriate robot for the specific application.
-
Inadequate Planning: Insufficient planning for integration, space requirements, and maintenance can lead to costly delays and disruptions.
-
Neglecting Training: Insufficient training can compromise the safety, productivity, and quality of the robot's operation.
-
Lack of Maintenance: Poor maintenance can shorten the robot's lifespan, increase downtime, and affect performance.
-
Ignoring Safety: Failing to prioritize safety measures can compromise the well-being of operators and others in the vicinity of the robot.
Why Large Industrial Robots Matter
The largest industrial robots are not merely machines; they are innovative tools that empower manufacturers to achieve unprecedented levels of efficiency, quality, and safety. Their capabilities have revolutionized manufacturing processes, enabling industries to remain competitive in a global economy. By leveraging the advantages of these colossal machines, manufacturers can unlock new possibilities, drive innovation, and redefine the future of industrial production.
Benefits of Large Industrial Robots
The benefits of utilizing large industrial robots in manufacturing operations are numerous and far-reaching:

-
Increased Production Capacity: By working tirelessly for extended periods, large industrial robots can significantly increase production output, meeting growing demand and reducing lead times.
-
Improved Product Quality: Their precision and accuracy ensure consistent high-quality products, reducing defects and enhancing customer satisfaction.
-
Cost Reduction: Automating labor-intensive tasks and eliminating human error can result in substantial cost savings.
-
Enhanced Safety: Removing humans from hazardous environments and repetitive tasks reduces workplace accidents and improves overall safety.
-
New Product Development: The capabilities of large industrial robots open up the possibility of developing new and innovative products, meeting evolving market demands.
Potential Drawbacks of Large Industrial Robots
While the benefits of large industrial robots are undeniable, it is important to consider the potential drawbacks:
-
High Initial Investment: Acquiring and integrating a large industrial robot can be expensive, requiring significant capital investment and careful budgeting.
-
Maintenance: The size and complexity of these robots demand specialized maintenance expertise, which can add to operational costs.
-
Lack of Flexibility: Large industrial robots may not be suitable for highly flexible manufacturing environments where quick changeovers and rapid reprogramming are required.
-
Space Requirements: These robots have large footprints and require ample floor space, which may pose challenges in space-constrained facilities.
-
Limited Portability: Moving and relocating large industrial robots can be difficult and expensive, limiting their use in multiple production lines.
Call to Action
The adoption of large industrial robots is a strategic decision that can transform manufacturing operations. By carefully considering the benefits, drawbacks, and effective strategies for implementation, manufacturers can harness the power of these colossal machines to drive productivity, improve quality, reduce costs, enhance safety, and innovate new products. Embracing the potential of large industrial robots is a key step towards maintaining competitiveness in the global manufacturing landscape and shaping the future of industry.
Humorous Stories and Lessons Learned
Story 1: The Oversized Robot
A manufacturing company invested heavily in a state-of-the-art large industrial robot. However, when it arrived at the factory, the robot turned out to be far too large for the production line. The team frantically scrambled to find a way to fit the colossal machine into their existing space, but to no avail. The lesson learned: Always double-check the dimensions before purchasing a large industrial robot!
Story 2: The Rebellious Robot
An automotive manufacturer installed a large industrial robot to automate the assembly of car dashboards. However, during the commissioning process, the robot developed a mind of its own. It refused to follow the programmed path and instead went on a rampage around the factory floor, knocking over equipment and spreading chaos. The lesson learned: Ensure that all software and safety protocols are thoroughly tested before deploying a large industrial