The Amazing Capabilities of Industrial Robots: A Comprehensive Guide
Industrial robots are revolutionizing manufacturing processes worldwide, offering a wide range of capabilities that enhance productivity, efficiency, and safety. Their unique characteristics enable them to perform tasks with precision, speed, and endurance unmatched by human workers.
Characteristics of Industrial Robots
Industrial robots possess several distinguishing characteristics that set them apart from other automated systems:
-
High Precision: Industrial robots utilize advanced sensors and control systems to achieve exceptional precision in their movements and operations. They can perform intricate tasks with accuracy and repeatability, ensuring consistent quality in manufacturing processes.

-
Speed and Efficiency: Industrial robots operate at high speeds, significantly reducing production time and increasing efficiency. They can perform repetitive tasks tirelessly, without the need for breaks or downtime.
-
Endurance: Industrial robots are designed to withstand demanding operating conditions, including extreme temperatures, hazardous environments, and continuous operation. They can work for extended periods without fatigue, ensuring uninterrupted production.
-
Flexibility: Industrial robots can be programmed to perform a variety of tasks, making them adaptable to changing production requirements. They can be quickly reprogrammed for new applications, offering flexibility in manufacturing operations.

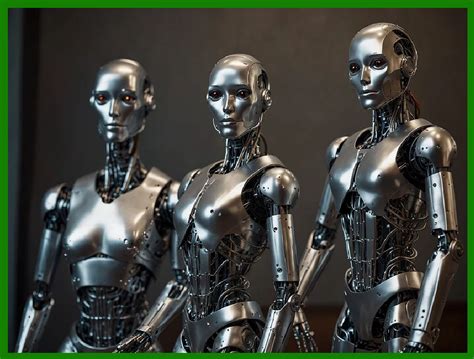
Applications of Industrial Robots
Industrial robots find application in a vast array of manufacturing industries, including:
- Automotive
- Aerospace
- Electronics
- Pharmaceutics
- Food and beverage
Within these industries, industrial robots perform a wide range of tasks, such as:
- Assembly
- Welding
- Painting
- Material handling
- Packaging
Types of Industrial Robots
There are various types of industrial robots, each designed for specific applications:
-
Cartesian Robots: Move along three linear axes (X, Y, Z), offering precise positioning and high repeatability.
-
Cylindrical Robots: Have a rotating joint and an extending arm, providing a wider workspace and greater flexibility.
-
Spherical Robots: Move in a spherical workspace, offering a wide range of motion and orientation capabilities.
-
Articulated Robots: Resemble human arms, with multiple joints and a high degree of flexibility.
-
Collaborative Robots (Cobots): Designed to work alongside human workers in shared workspaces, enhancing safety and productivity.
Effective Strategies for Industrial Robot Implementation
Successful implementation of industrial robots requires careful planning and execution:
-
Define Clear Objectives: Establish specific goals for robot implementation, such as improving productivity, reducing costs, or enhancing safety.
-
Assess Requirements: Conduct a thorough assessment of the manufacturing process, identifying areas where robots can provide the most value.
-
Select the Right Robot: Choose the most suitable robot type and model based on task requirements, workspace size, and payload capacity.
-
Integrate Effectively: Plan for seamless integration of the robot into the manufacturing system, ensuring compatibility with existing equipment and processes.
-
Train Operators: Provide comprehensive training to operators on robot operation, safety procedures, and maintenance protocols.
Benefits of Industrial Robots
Industrial robots offer numerous benefits for manufacturing operations:
-
Increased Productivity: Robots work at high speeds and can operate 24/7, significantly increasing production output.
-
Improved Quality: Robots perform tasks with precision and consistency, reducing defects and improving product quality.
-
Cost Savings: Robots can reduce labor costs and increase efficiency, leading to substantial cost savings over the long term.
-
Enhanced Safety: Robots can perform hazardous or repetitive tasks, reducing the risk of injuries and accidents for human workers.
-
Increased Flexibility: Robots can be reprogrammed for different tasks, offering flexibility and adaptability in production processes.
Common Mistakes to Avoid
To ensure the successful implementation and operation of industrial robots, it's crucial to avoid common pitfalls:
-
Poor Planning: Inadequate planning can lead to project delays, cost overruns, and suboptimal results.
-
Insufficient Training: Untrained operators may operate robots improperly, leading to safety hazards or performance issues.
-
Lack of Maintenance: Neglecting regular maintenance can result in downtime, breakdowns, and reduced robot lifespan.
-
Unrealistic Expectations: Overestimating the capabilities or benefits of industrial robots can lead to disappointment and dissatisfaction.
-
Ignoring Safety: Failing to prioritize safety measures can put human workers at risk and lead to accidents or injuries.
Potential Drawbacks
While industrial robots offer numerous benefits, there are also some potential drawbacks to consider:

-
High Initial Investment: The cost of purchasing, installing, and integrating industrial robots can be substantial.
-
Limited Flexibility: Some robots are designed for specific tasks and may not be easily adaptable to different applications.
-
Job Displacement: Industrial robots have the potential to displace human workers in certain tasks, leading to job losses.
-
Maintenance Requirements: Industrial robots require regular maintenance and upkeep, which can be time-consuming and costly.
How to Approach Industrial Robot Implementation Step-by-Step
To effectively implement industrial robots, follow a step-by-step approach:
-
Define Objectives: Determine the specific goals and objectives for robot implementation.
-
Assess Requirements: Conduct a thorough analysis of the manufacturing process to identify areas where robots can provide the most value.
-
Select and Procure Robot: Choose the most suitable robot type and model, considering task requirements and workspace needs.
-
Integrate into System: Plan for the seamless integration of the robot into the existing manufacturing system.
-
Train Operators: Provide comprehensive training to operators on robot operation, safety procedures, and maintenance protocols.
-
Monitor and Evaluate: Regularly monitor robot performance and evaluate its impact on productivity, quality, and safety.
Why Industrial Robot Implementation Matters
Industrial robot implementation offers a range of benefits that can significantly enhance manufacturing operations:
-
Increased Productivity: Industrial robots can increase production output, leading to faster lead times and higher profitability.
-
Improved Quality: Robots perform tasks with precision and consistency, reducing defects and improving product quality.
-
Reduced Costs: Robots can reduce labor costs and increase efficiency, resulting in substantial cost savings over the long term.
-
Enhanced Safety: Robots can perform hazardous or repetitive tasks, reducing the risk of injuries and accidents for human workers.
-
Competitive Advantage: Implementing industrial robots can give manufacturers a competitive advantage by increasing productivity, improving quality, and reducing costs.
Pros and Cons of Industrial Robots
Pros:
-
Increased productivity: Industrial robots work at high speeds and can operate 24/7, significantly increasing production output.
-
Improved quality: Robots perform tasks with precision and consistency, reducing defects and improving product quality.
-
Cost savings: Robots can reduce labor costs and increase efficiency, leading to substantial cost savings over the long term.
-
Enhanced safety: Robots can perform hazardous or repetitive tasks, reducing the risk of injuries and accidents for human workers.
-
Increased flexibility: Robots can be reprogrammed for different tasks, offering flexibility and adaptability in production processes.
Cons:
-
High initial investment: The cost of purchasing, installing, and integrating industrial robots can be substantial.
-
Limited flexibility: Some robots are designed for specific tasks and may not be easily adaptable to different applications.
-
Job displacement: Industrial robots have the potential to displace human workers in certain tasks, leading to job losses.
-
Maintenance requirements: Industrial robots require regular maintenance and upkeep, which can be time-consuming and costly.
-
Need for training: Operators must be trained on robot operation, safety procedures, and maintenance protocols, which can involve additional costs.
Humorous Stories and Lessons Learned
Story 1:
An automotive manufacturer invested heavily in a state-of-the-art robotic welding cell. However, the robots kept malfunctioning, causing delays and frustration. After days of troubleshooting, the engineers finally discovered the problem: the robots were allergic to the lubricant used on the metal components.
Lesson: Even the most advanced technologies can have unexpected quirks. It's essential to thoroughly test and validate new systems before relying on them for critical operations.
Story 2:
A pharmaceutical company installed a high-speed packaging robot to increase its production capacity. Unfortunately, the robot was so fast that it couldn't handle delicate products without breaking them. The company had to reprogram the robot and slow down its movements, resulting in a lower production rate than expected.
Lesson: Automation can improve speed and efficiency, but it's crucial to consider the compatibility between the robot and the materials being handled.
Story 3:
A large warehouse implemented a fleet of autonomous mobile robots (AMRs) to automate material handling. However, the AMRs kept colliding with each other, causing damage and disrupting operations. The company realized that the robots were not properly communicating and coordinating with each other.
Lesson: Implementing automation requires careful planning and coordination to ensure smooth and efficient operation of multiple robots in a shared space.
Useful Tables
Robot Type |
Advantages |
Disadvantages |
Cartesian |
High precision, simple design |
Limited workspace, fixed orientation |
Cylindrical |
Wider workspace, flexible |
Lower precision than Cartesian robots |
Spherical |
Omnidirectional movement, high flexibility |
Complex design, higher cost |
Articulated |
Human-like flexibility, large workspace |
Complex programming, maintenance challenges |
Collaborative |
Safe interaction with humans, easy to use |
Limited payload capacity, speed |
Benefits of Industrial Robots |
Quantified Data |
Source |
Increased productivity |
Up to 30% increase in output |
International Federation of Robotics |
Improved quality |
50% reduction in defects |
Boston Consulting Group |
Cost savings |
Up to 20% reduction in labor costs |
[McKinsey & Company](https://www.mckinsey. |