Colossal Titans: Unveiling the Giants of Industrial Robotics
In the colossal arena of industrial automation, where precision and efficiency reign supreme, a select few titans stand tall as the leading manufacturers of industrial robots. These behemoths drive the pulse of modern manufacturing, empowering industries with unparalleled productivity, flexibility, and precision.
Giants of the Industry: Market Dominators
The global industrial robotics market is colossal, projected to soar past $74 billion by 2025. Within this vast landscape, a handful of behemoths dominate the scene:
1. Fanuc Corporation

-
Revenue: $5.2 billion
-
Market share: 30%
-
Headquartered in: Japan
-
Specialization: High-precision robots for automotive and electronics manufacturing
2. ABB
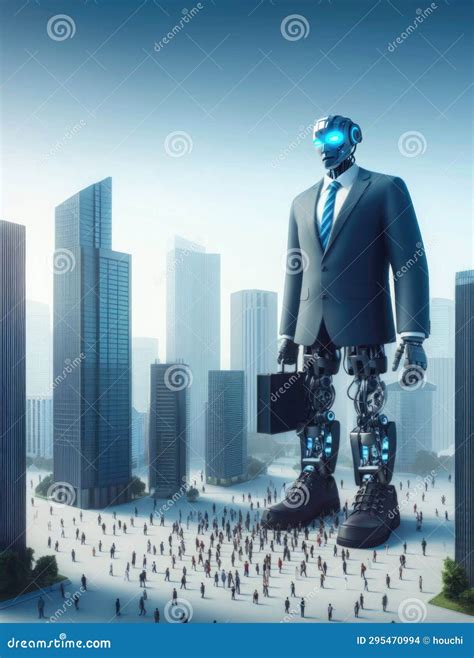
-
Revenue: $2.8 billion
-
Market share: 16%
-
Headquartered in: Switzerland
-
Specialization: Collaborative robots and systems integration
3. Yaskawa Electric Corporation
-
Revenue: $2.6 billion
-
Market share: 15%
-
Headquartered in: Japan
-
Specialization: Robotics for welding, painting, and assembly
4. Kawasaki Heavy Industries

-
Revenue: $1.9 billion
-
Market share: 11%
-
Headquartered in: Japan
-
Specialization: Heavy-duty robots for shipbuilding and aerospace
The Journey to Automation: Case Studies
The transformative power of industrial robots is evident in countless success stories:
-
Ford Motor Company: Implemented 800 robots in a Kentucky plant, resulting in a 40% increase in production efficiency.
-
Amazon Robotics: Developed a fleet of autonomous mobile robots, enabling the fulfillment of 100 million orders per year.
-
Toyota Motor Corporation: Unleashed a new generation of collaborative robots, fostering seamless human-machine interaction on the assembly line.
Humorous Tales from the Robot Revolution
In the midst of the industrial revolution, even the most formidable of robots can experience amusing mishaps:
-
The Clumsy Conveyor: A robot tasked with loading parts onto a conveyor belt mistook a human worker's hand for a product, gingerly placing it on the line.
-
The Armless Automaton: During a power outage, a robot lost its robotic arm, resembling a bewildered mannequin until power was restored.
-
The Clean-Up Crew: A robot vacuum intended to clean a dusty warehouse accidentally aspirated a supervisor's toupee, leaving him bald but amused.
Why Industrial Robots Matter: Unlocking Benefits
Industrial robots are not mere machines; they are catalysts for transformative benefits:
-
Enhanced Productivity: Robots work tirelessly, repeating tasks with unwavering accuracy, boosting production rates and reducing lead times.
-
Improved Quality: Automated processes minimize human error, ensuring consistent and impeccable product quality.
-
Reduced Labor Costs: While robots may require an initial investment, they ultimately reduce labor expenses by automating repetitive and hazardous tasks.
-
Increased Flexibility: Robots can be reprogrammed for different tasks, enabling manufacturers to adapt to changing market demands.
-
Improved Safety: Removing humans from hazardous tasks reduces workplace accidents and improves safety conditions.
Advanced Features: Cutting-Edge Capabilities
Modern industrial robots boast an array of advanced features:
-
AI-Powered Vision Systems: Enhance precision and enable the identification of complex objects.
-
Collaborative Functionality: Facilitate seamless human-robot interaction for increased efficiency and safety.
-
Cloud Connectivity: Enable remote monitoring, diagnostics, and software updates for enhanced reliability.
-
Modular Design: Allow for customization and adaptability to specific application needs.
-
Multi-Axis Articulation: Provide exceptional flexibility and precision for complex tasks.
Pros and Cons: Evaluating the Advantages and Limitations
Like any technology, industrial robots have their advantages and drawbacks:
Pros:
- Increased productivity
- Improved quality
- Reduced labor costs
- Enhanced flexibility
- Improved safety
Cons:
- High initial investment
- Job displacement concerns
- Maintenance and repair costs
- Training requirements
- Limited creativity and problem-solving abilities
Tips and Tricks: Maximizing Robot Efficiency
-
Task Analysis: Conduct a thorough analysis of tasks to identify those best suited for automation.
-
Robot Selection: Carefully select robots based on capabilities, payload capacity, and application-specific requirements.
-
Proper Maintenance: Regularly inspect, clean, and lubricate robots to ensure optimal performance and longevity.
-
Operator Training: Provide comprehensive training to operators to ensure safe and effective robot operation.
-
Safety Precautions: Implement proper safety measures, including physical barriers and emergency stop buttons.
Common Mistakes to Avoid: Pitfalls to Steer Clear Of
-
Overestimating Capabilities: Avoid assigning tasks that exceed the robot's capabilities and limitations.
-
Neglecting Maintenance: Failure to maintain robots can result in breakdowns, costly repairs, and reduced productivity.
-
Underutilizing Features: Explore and leverage the advanced features of robots to maximize their potential.
-
Inadequate Training: Untrained operators can compromise safety and limit robot efficiency.
-
Ignoring Safety Measures: Overlooking safety protocols can lead to accidents and liability issues.
FAQs: Uncovering Common Questions
-
What are the different types of industrial robots?
Industrial robots vary in size, shape, payload capacity, and capabilities, ranging from articulated robots to collaborative robots.
-
How much do industrial robots cost?
The cost of industrial robots varies widely depending on their features and capabilities, starting from a few thousand dollars to hundreds of thousands of dollars.
-
How long does it take to implement an industrial robot?
The implementation timeframe varies depending on factors such as the complexity of the application and the robot's delivery time, typically ranging from a few months to a year.
-
Do industrial robots require programming?
Depending on the complexity of the task, industrial robots may require programming using specialized software.
-
What are the future trends in industrial robotics?
Emerging trends include the integration of AI, cloud connectivity, and collaborative robotics for enhanced automation and efficiency.
-
What is the future outlook for industrial robots?
The market for industrial robots is projected to continue its robust growth, driven by increasing adoption across industries and advancements in technology.
-
How do I choose the right industrial robot for my application?
To select the optimal robot, consider factors such as payload capacity, accuracy, speed, and the specific tasks you need to automate.
-
Where can I find more information on industrial robots?
Authoritative sources for additional information include the International Federation of Robotics (IFR) and the Robotic Industries Association (RIA).